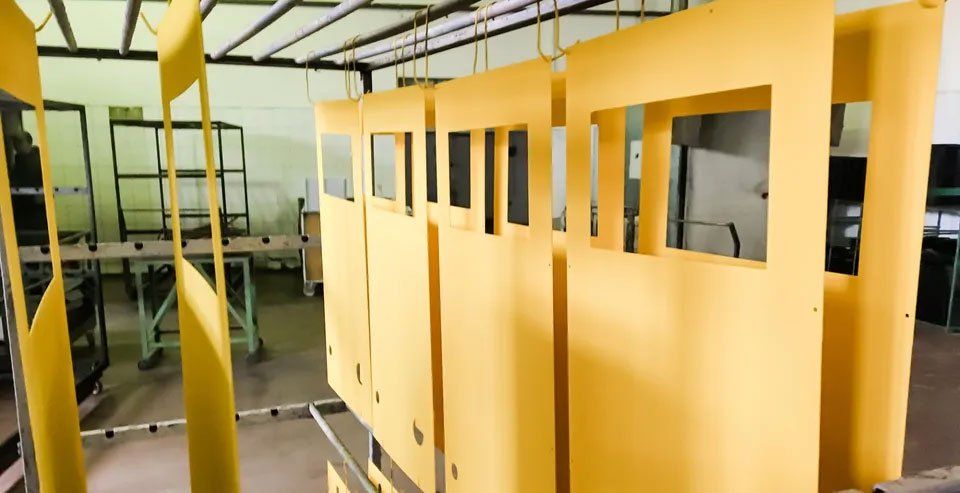
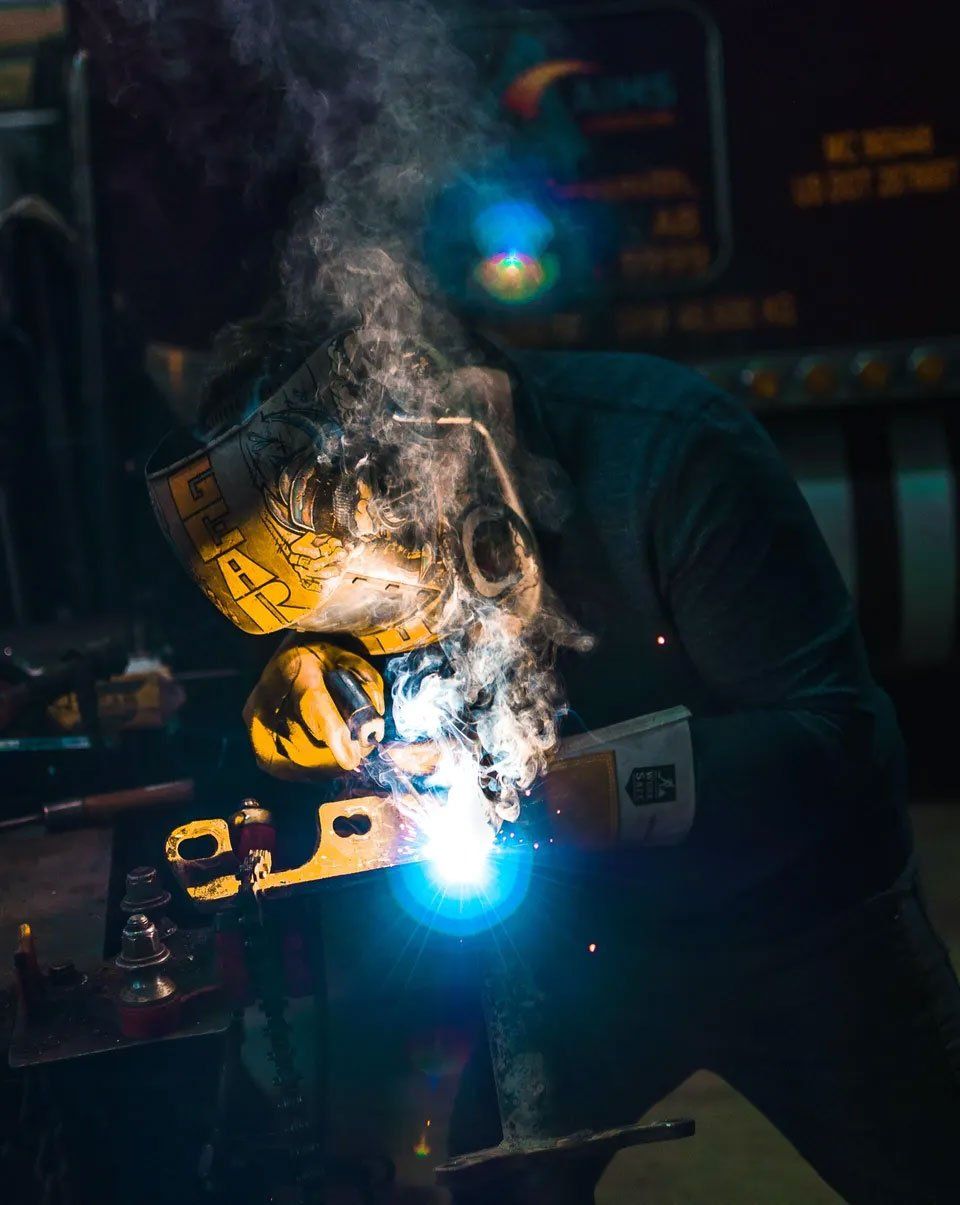
Metal fabrication projects that use welding processes will usually experience at least some degree of welding distortion. Distortion in a weld results from the expansion and contraction of the weld metal and base metal during the heating and cooling cycle of the welding process. During the heating and cooling cycle, many factors affect the shrinkage of the metal and lead to distortion, such as physical and mechanical properties that change as heat is applied.
Distortion is an issue for multiple reasons, but one of the most critical is the potential of a weld that is not structurally sound. Welding distortions can threaten the structural integrity and/or the aesthetic of a project. Depending on the type and size of the distortion and the material used there are different corrective techniques that can be used to fix weld distortions.
Factors such as the type of metal, the amount of residual stress, and the degree of restraining used during the welding process impact the amount of distortion and the type of distortion. Here are some of the common types of welding distortions:
If you are looking for a reliable machine shop to assist you with a metal fabrication project, turn to Midland Waterjet. No matter your needs, we will handle everything from waterjet cutting, bending, and assembly, to welding. Our machine shop has the capability to work with a range of materials including steel, aluminum, copper, titanium, brass, cast iron, and so much more. For years, our machine shop has provided top-notch metal fabrication for clients across Midland, Odessa, Lubbock, Abilene, TX and the surrounding regions.
While we’re proud to offer quality metal fabrication solutions, we also have experience with stone, glass, wood, laminate, composite, and plastic fabrication services. If you’re interested in learning more, don’t waste another moment.
Contact our machine shop to get started on your next fabrication project!
Proudly Serving
Web Design by LocalEdge, all rights reserved | Sitemap